Global O&G leader automates inventory audits to drive process excellence
The Challenge
The customer faced several operational and logistical challenges in inventory audits at different sites. This made it risky for the employees to approach the equipment and perform necessary checks. The audit process that the company performed was time-consuming and manually intensive, requiring individuals to inspect each piece of equipment separately.
Another major challenge faced was the manual process of reporting and reconciliation procedures. The process was cumbersome and prone to errors, further complicating the task of maintaining accurate records. In their quest for a partner capable of delivering a transformative impact through material visibility, tracking and management, the customer turned to HCLTech for a comprehensive solution.
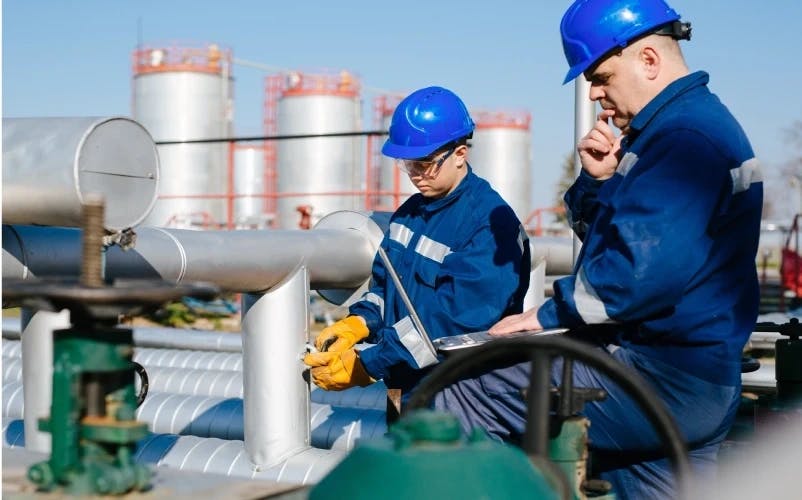
The Objective
Reduce manual work:
The existing audit process of the customer was performed manually, requiring the employees to physically check each piece of equipment to perform the audit. This method was not only time-consuming but also prone to human error. Automating this process aimed to significantly cut down on the time and effort required for audits, making the process more efficient and less labor-intensive
Implementing omni-tracking solution for long-distance tag reading:
The client sought to implement a robust asset management system by mounting RFID fixwed readers on moving trucks and assets equipped with RFID tags. However, a key challenge arose in reading the tags from a distance of 30 meters, even though RFID technology was well-suited for their needs.
Given the highly inflammable and sensitive nature of their sites, sucj as oil refinery and rigs, the solution required ATEX certification to ensure compliance with safety standards. HCLTech provided a comprehensive omni-tracking solution that integrated passive RFIDs, barcodes and BLE effectively addressing the client’s requirement while meeting all compliance and safety needs
Improve safety:
Conducting manual audits in remote and hazardous environments posed significant safety risks to the personnel involved. By implementing a solution that minimizes the need for human presence in these areas, the project aimed to enhance the overall safety of the operations. The use of radio frequency identification (RFID) technology and Bluetooth energy usage (BLE) allowed for the tracking and monitoring of assets from a safe distance, reducing the exposure of workers to potentially dangerous conditions
Enhance efficiency in tracking and reporting:
The manual process of tracking and reconciling assets was not only error-prone but also cumbersome. The objective was to streamline this process by leveraging technology to automate the data collection and reporting. This would ensure more accurate tracking of assets, quicker data processing, and more reliable reporting, ultimately leading to better asset management and operational efficiency
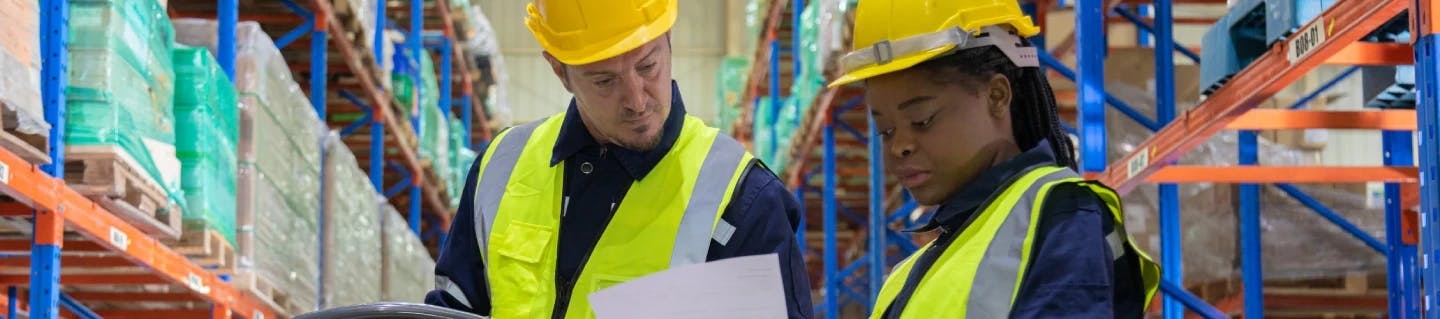
The Solution
To address these challenges, the Industry NeXT and IoT team at HCLTech conducted a design thinking workshop and visited the customer location to gain a deeper understanding of the issues at hand. They developed an engagement journey roadmap and created a high-level architecture for the solution.
- HCLTech deployed the Track and Trace for Field Assets powered by IATM to design a high-level architecture for an omni tracking solution comprising of RFID, BLE and Barcode solution in collaboration with the customer
- RFID fixed readers were mounted on moving trucks to track assets tagged with ATEX-certified RFID tags, effectively overcoming the challenge in reading tags from a distance of 30 meters
- Conducted analysis to determine how effectively the fixed readers could be mounted on the trucks and evaluated the performance of the fixed readers in real-world conditions
- Integration with construction, remediation, reclamation and facilities management information system
- Developed an application to process data collected by the fixed readers. The application compared collected data to identify any missing assets and provided summary reports
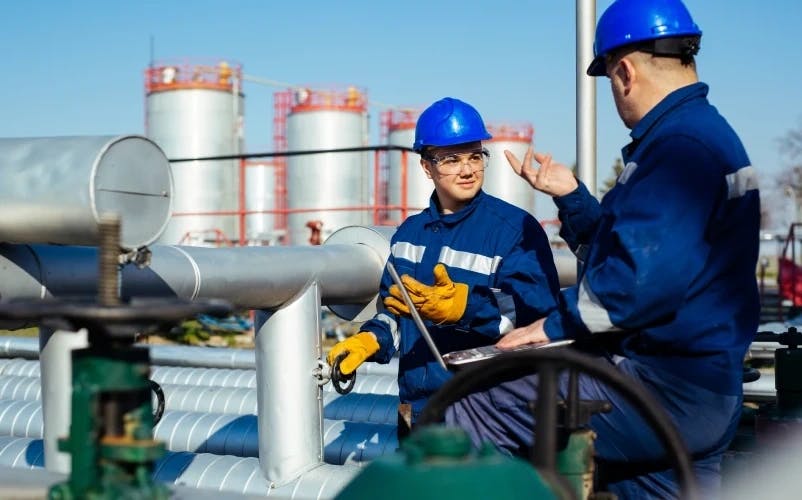
The Impact
- 90% time reduction in manual audit for fixed assets at remote sites
- Achievement of enhanced safety by maintaining distance from the equipment containing hazardous materials
- Improvement in productivity and efficiency through automated reporting and integration
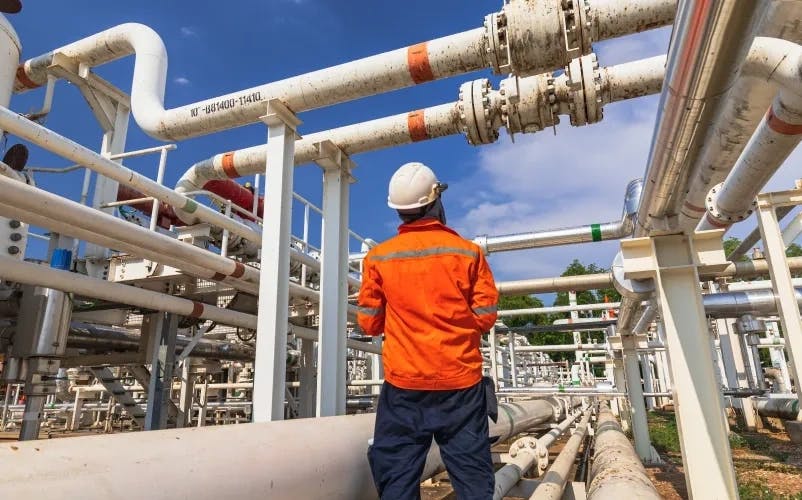